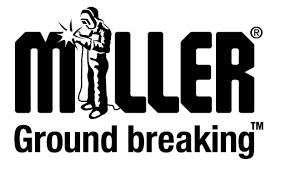
Earthmoving Attachments Specialist Invests in Next Generation of Robotic Automation and Collaborative Working
The UK’s largest bucket and coupler manufacturer – Miller UK – has significantly bolstered its manufacturing capabilities through upgrading its suite of state-of-the-art welding robots significantly increasing production and the safety of its workforce.
With headquarters in the North East – and operations across the globe – Miller has invested in five new robots commissioned and already in full operation, allowing the firm to significantly improve its welding speed and deliver 100% weld consistencies on its product range.
The new robots are developed by industry leaders in welding and automation, CLOOS and include two different model ranges, QRC 410-2.0, ideal for welding attachments for machines up to 45 tonne and two QRC 350-E models, capable of handling attachments for machines up to 100T.
The company first invested in its welding robot range in 2018, with the first installation of the smaller robots. Recognising the value of these machines, Miller has now installed the latest range of these models with the introduction of two of the larger sized machines which doubles the company’s production capabilities.
And the business believes that it is the very first of its type across the globe to have such advanced robotic welding machinery capable to produce buckets with an impressive width of up to 3.2m with the ability to hold up to 4.5T of material which the larger robots offer.
Speaking about the investment, James Ross, Commercial Director at Miller said:
“Manufacturing technology has always been a priority and it is very important that Miller continues to invest in the next generation of welding equipment and robotic automation which can transform the quality to consistent market leading levels. This will be recognised by our customers in terms of product durability and performance in the field.
“With minimal production downtime required, and the ability to operate for extended periods of time, this has significantly increased our manufacturing capabilities – particularly to produce much larger buckets for extreme applications - to meet our demand and significantly reduce our lead times for customers. As such, this allows Miller to have a real competitive advantage in our marketplace.”
The QRC 350-E robot model boasts a range of smart features. Comprising 12 axis movement, including the robot arm, the machine is designed to allow for more manipulation of parts, which increases its versatility and ability to reach more difficult areas on a workpiece. This allows Miller to weld more, whilst reducing the manual labour required once the robot process has been completed.
The tandem and single torch of the machine operate in conjunction with each other with the tandem torch being used for long straight run welds whilst the single torch completes trickier, harder to reach radius parts. Working in synergy, not only does this increase the speed of the process, whilst reducing weld times because of its high deposition rate, it also reduces heat input decreasing distortion of the workpiece.
Gregg Hudson, Global Manufacturing Leader said: “The new robot really does step our production capabilities up to the next level. The weld finish achieved from this machine is exceptional – and like nothing else you will see on the market – as we continue to drive our quality standards, which is what we are known for. This is showcased with our demo units at Miller HQ where customers can inspect first hand the quality they will receive.
“It is an exciting time at Miller for our staff on the shop floor to work with the new machinery and learn the next generation of pre-programming welding automation techniques to operate the equipment, whilst continually developing their manual skills. We have significantly invested in upskilling our workforce with complex technical knowhow to operate our suite of robots and have a dedicated team for collaborative automated production.”
Increasing the safety of its workforce, the robot has an extensive range of safety features, including mechanical barriers closing when the robot is in use, which will further trigger an emergency stop if this was opened.
Established in 1978, Miller UK is a privately owned international company supplying its trusted products to a wide range of leading earthmoving manufacturers, including the likes of Komatsu, Hitachi, Volvo, Sany, LiuGong, Kubota, Case, Cat, and JCB as well as an established independent global distributor network and end users worldwide. The company prides itself on constantly pushing technology boundaries to ensure its earthmoving attachments are at the very forefront of safety standards and efficiency.